It's in the detail project
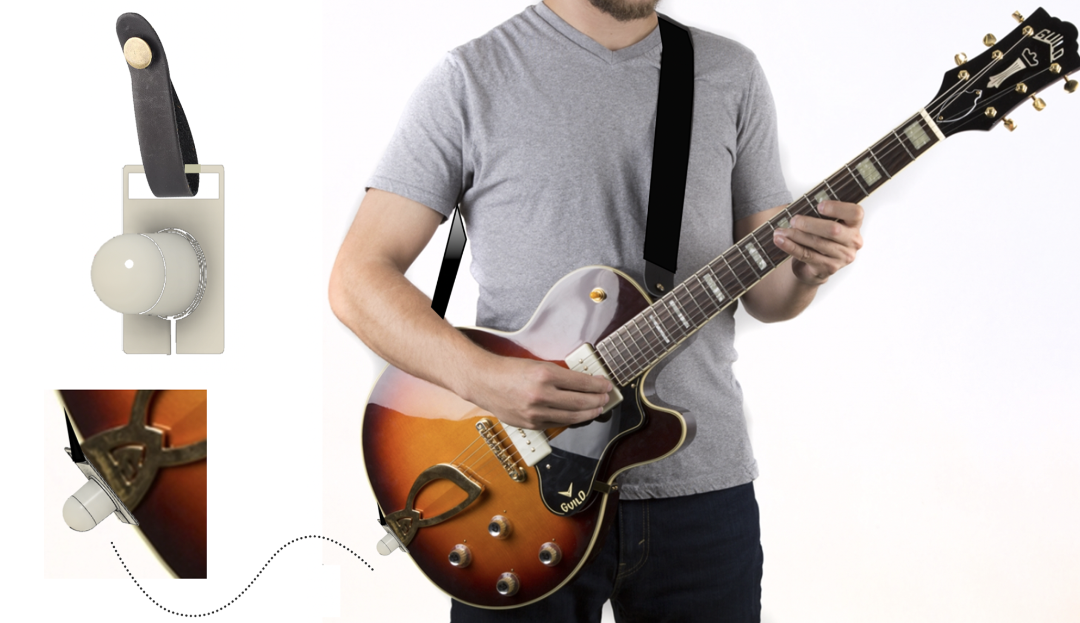
Brief
For this project we had to practice design for manufacture while considering a range of limitations such as manufacturing processes, material selection, surface finishes, tolerances, costing and engagement with other off-the-shelf components. We firstly had to identify an industry and product segment to design an object within the size range of <200mm. I chose to focus on music, in particular guitar accessories.
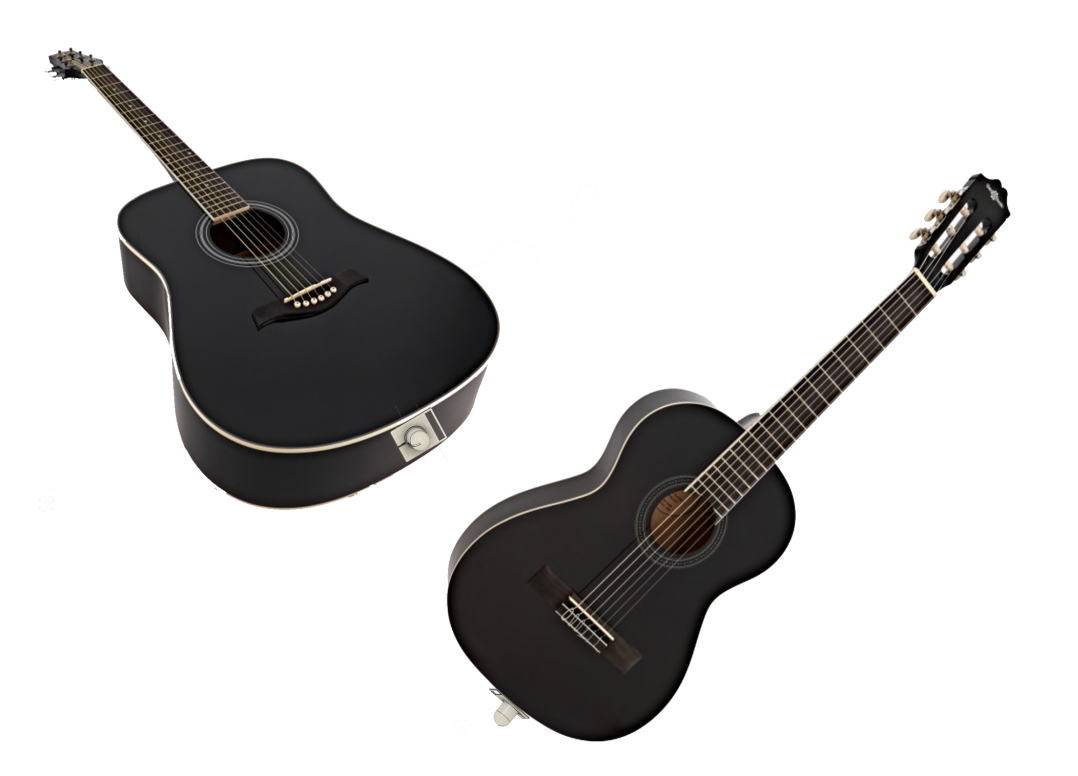
Research
I examined current guitars, straps, strap locks and endpins on the market and found that the existing mechanisms consist of an endpin screwed into the base of a guitar (which doesn't automatically come attached to every guitar) which allows for a standard guitar strap with a slit or hole in the end to be pushed over and trusted to fit and hold. Therefore I wanted to make a detachable guitar strap lock that wouldn't need to be screwed into and therefore potentially damaging or devaluing guitars, for the casual creative guitar player to enable easy transport and carrying of their guitar.
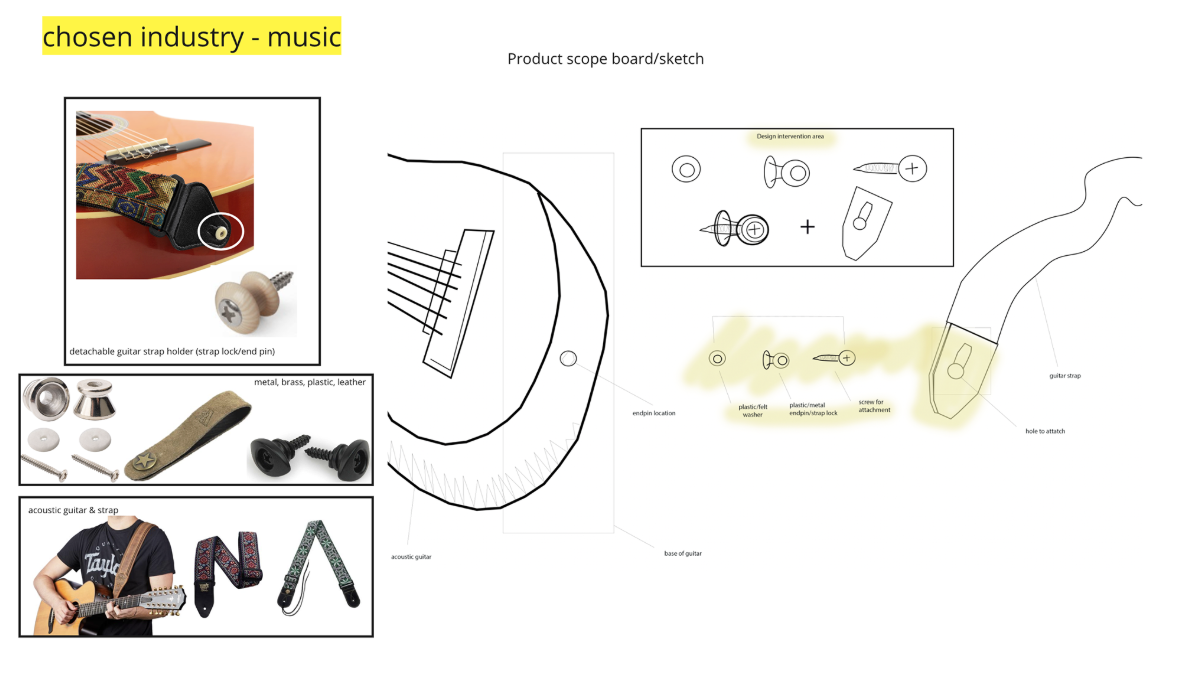
Concepts
I decided to combine the end lock and strap end therefore designing two components compatible with each other. My first concept is a snap fit, concept two is a push fit lock, while concepts three and four are slide/twist and snap fit . I also experimented with AI programs for conceptualising while it wasn't very helpful in generating new ideas it was fun to familiarise myself with new technology. I then made quick sketch models for each concept to examine size and validity of each mechanism and decided to proceed with concept one-'snap'.
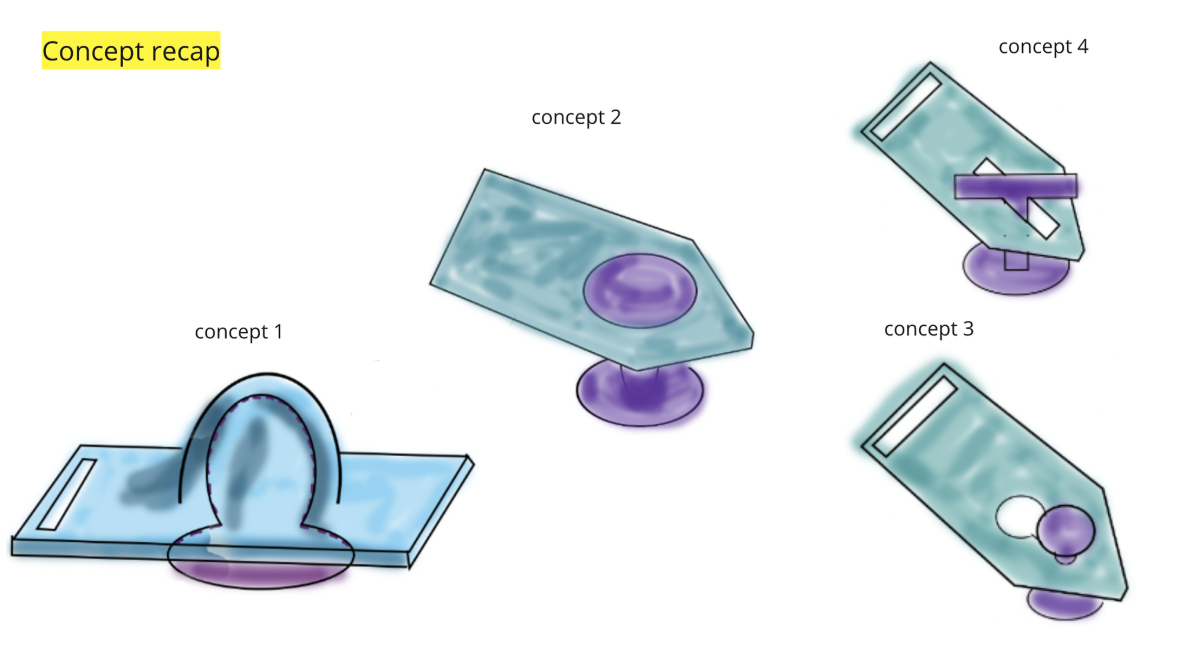
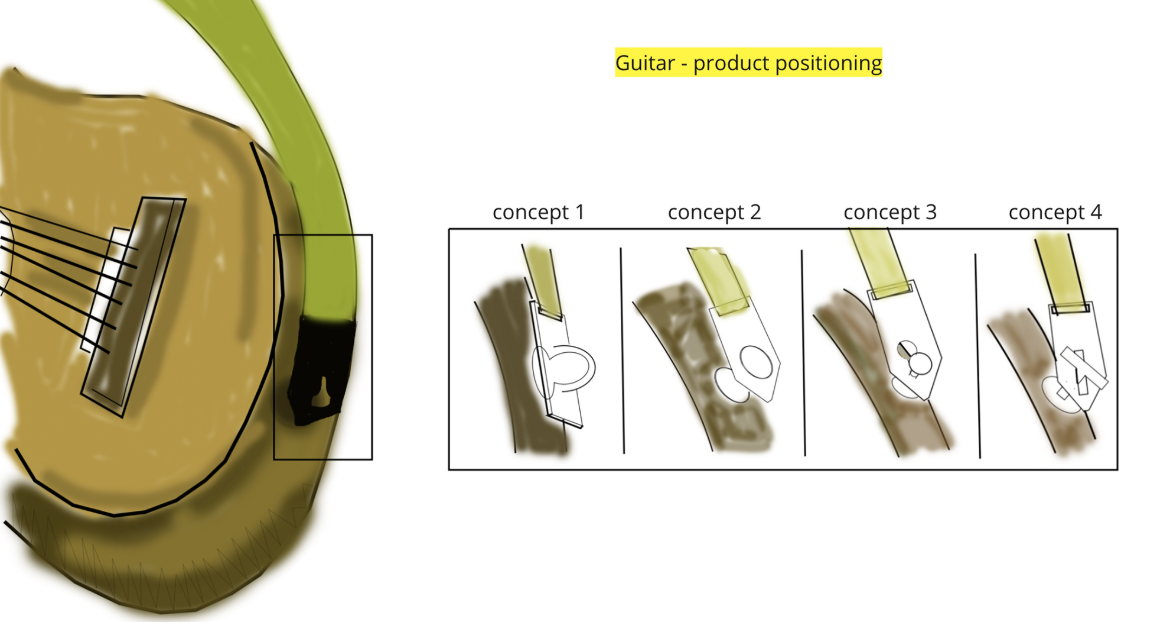
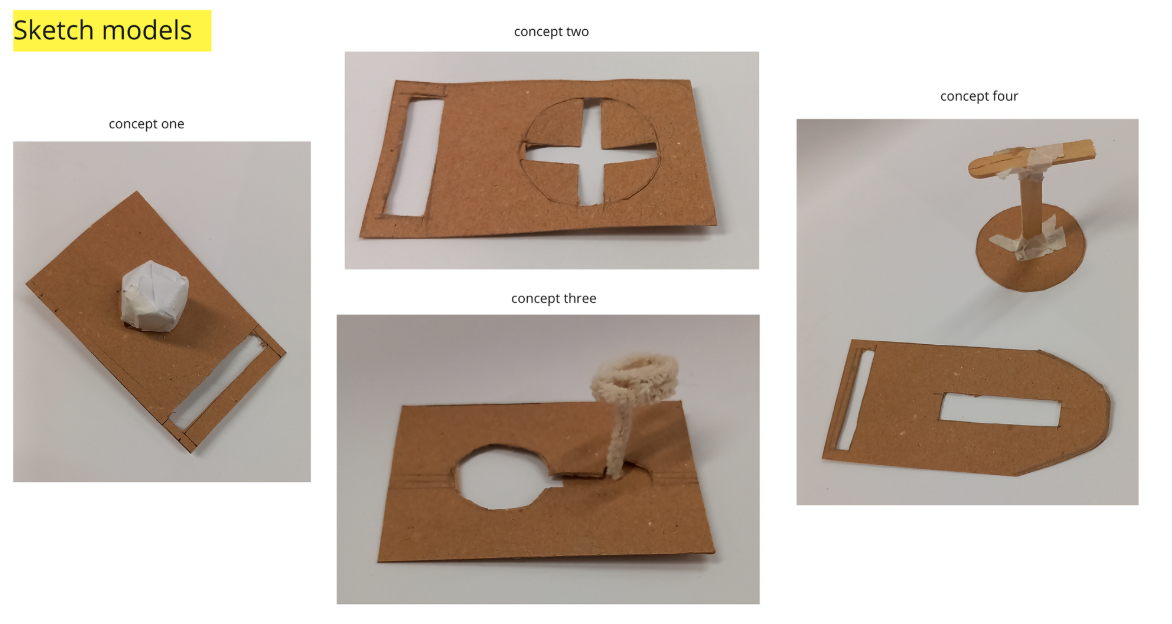
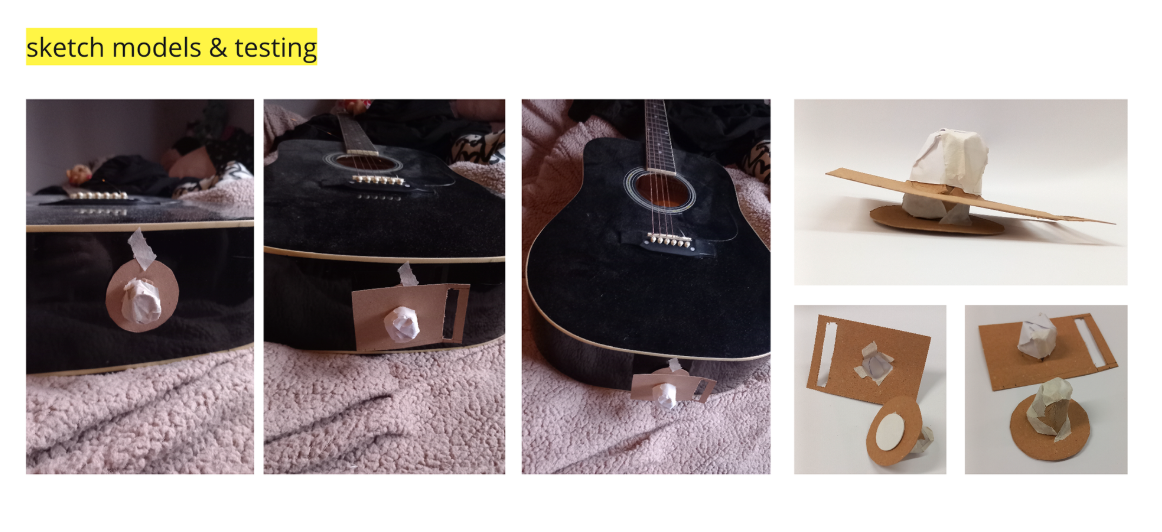
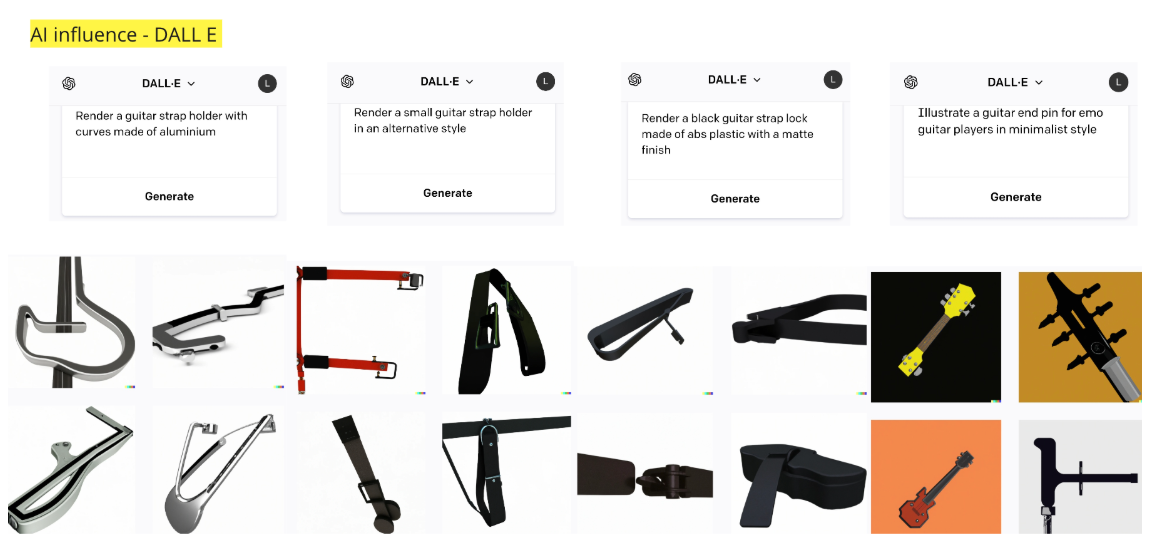
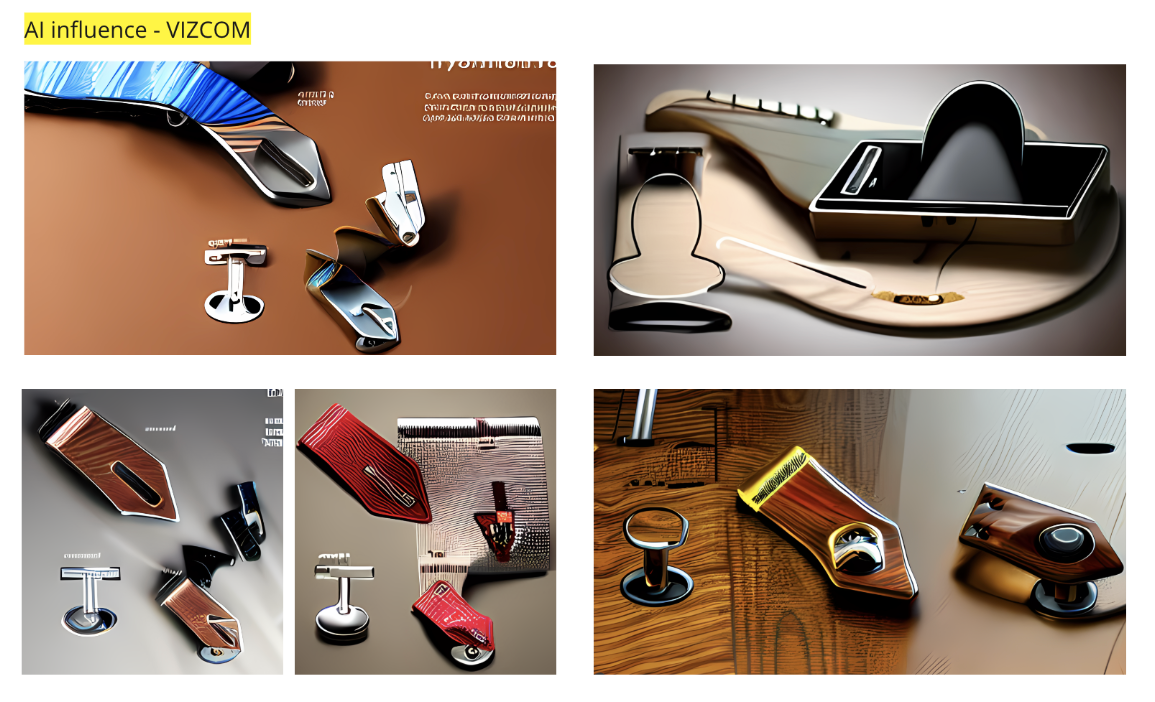
Development
Proceeding with concept one - 'snap' I sketched multiple sizes and shapes and decided to go with a rounded rectangular base shape for the female component and experimented with a range of rounded male components.
I found sketch modelling extremely useful in testing and defining my concept as it gave me a better understanding of the effects of undercutting depths and widths needed to ensure the two components fit together and also allowed me to experiment with how exactly the two components (made through vacforming initial foam models) would join and separate, for example I created a snug notch for one of the prototypes and cut a small slit for another prototype to see which would be more effective in combining the two components.
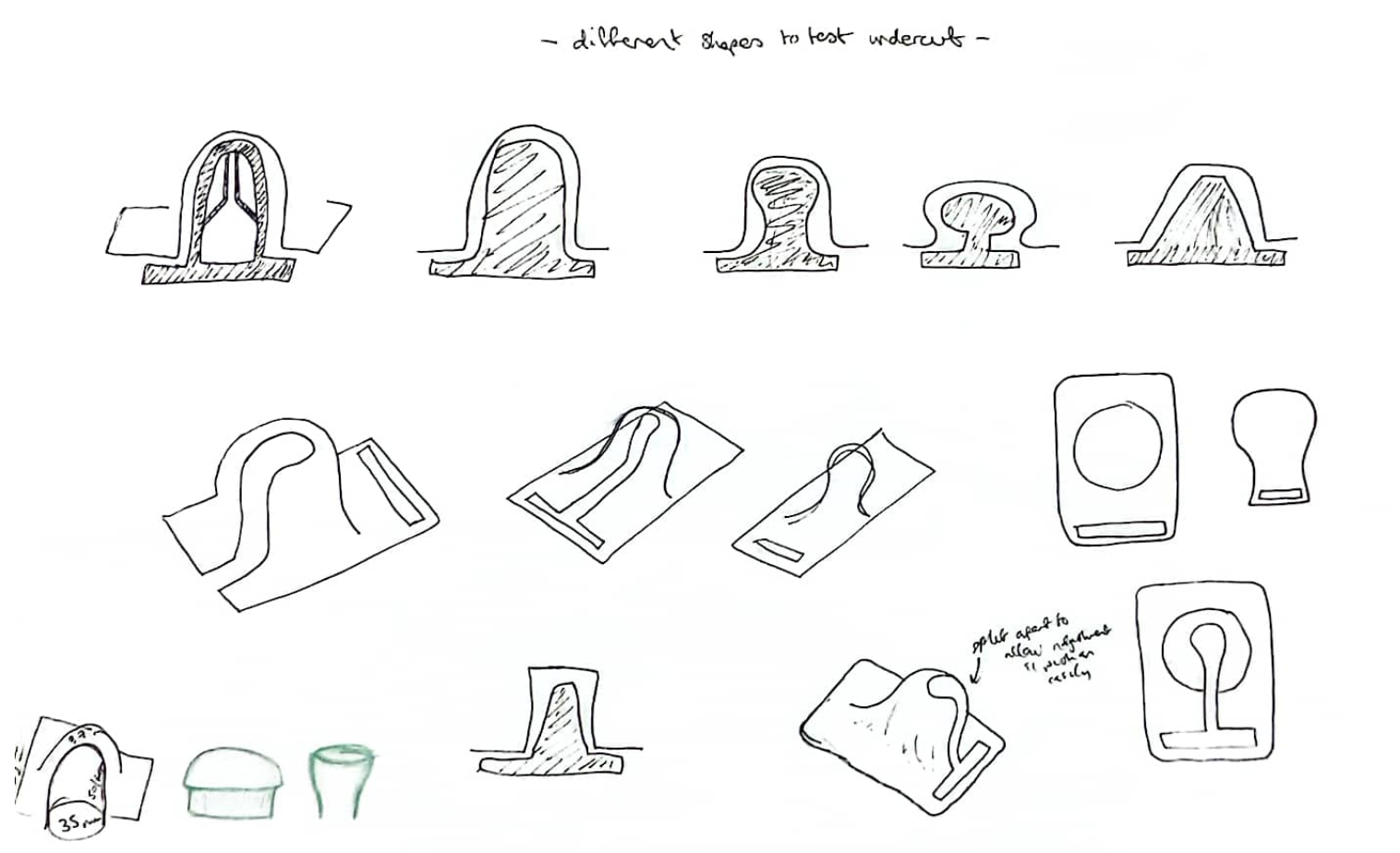
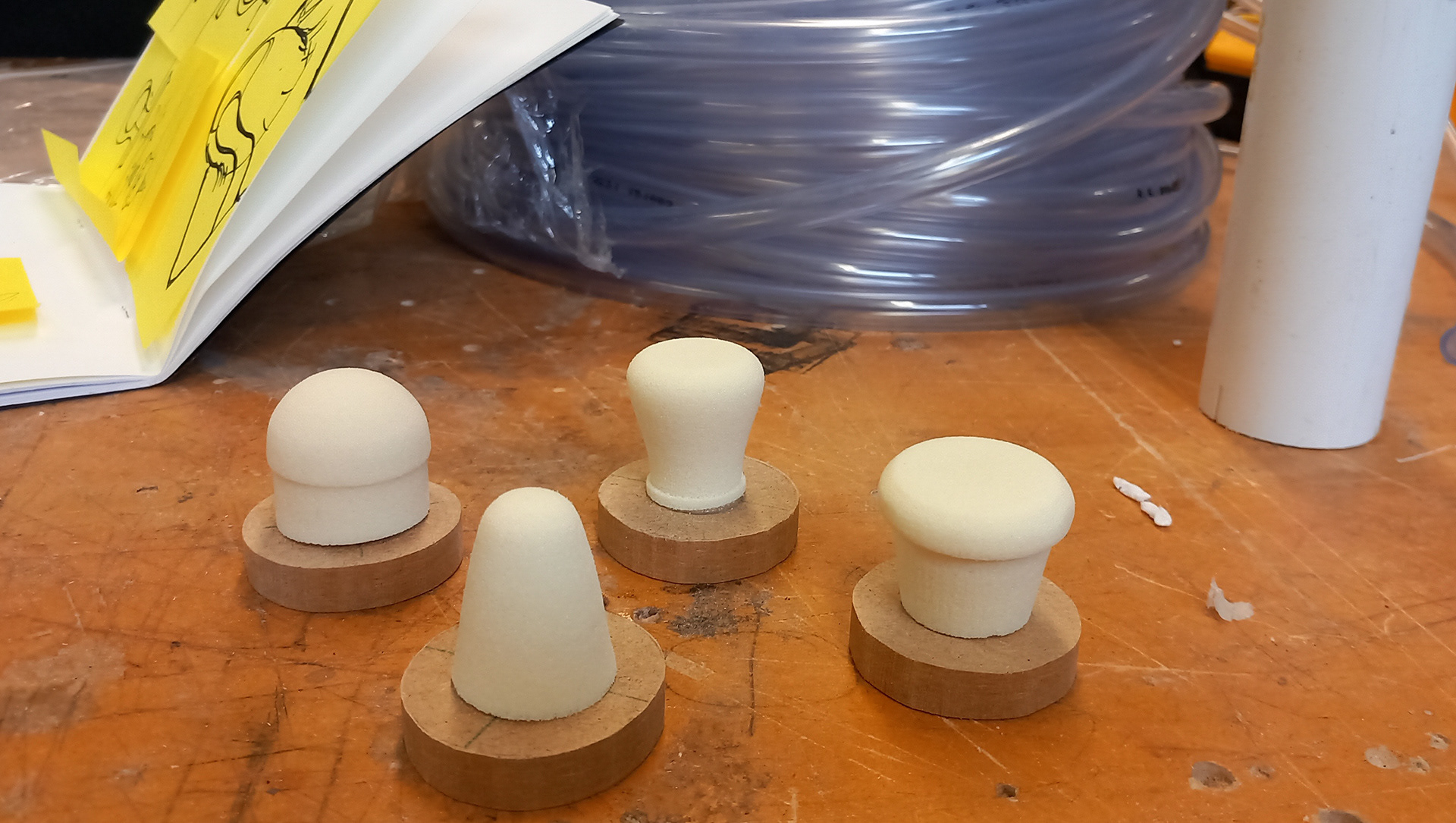
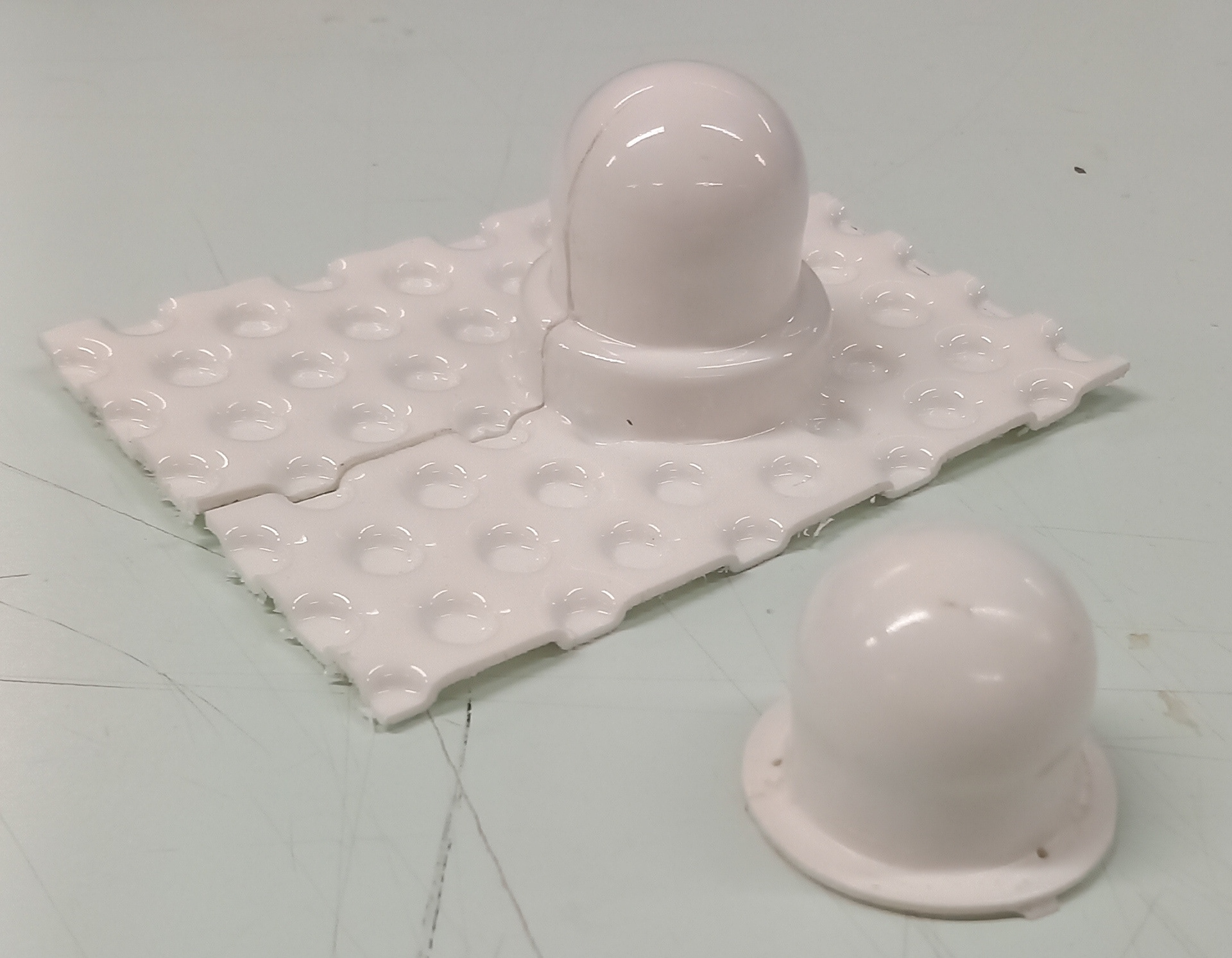
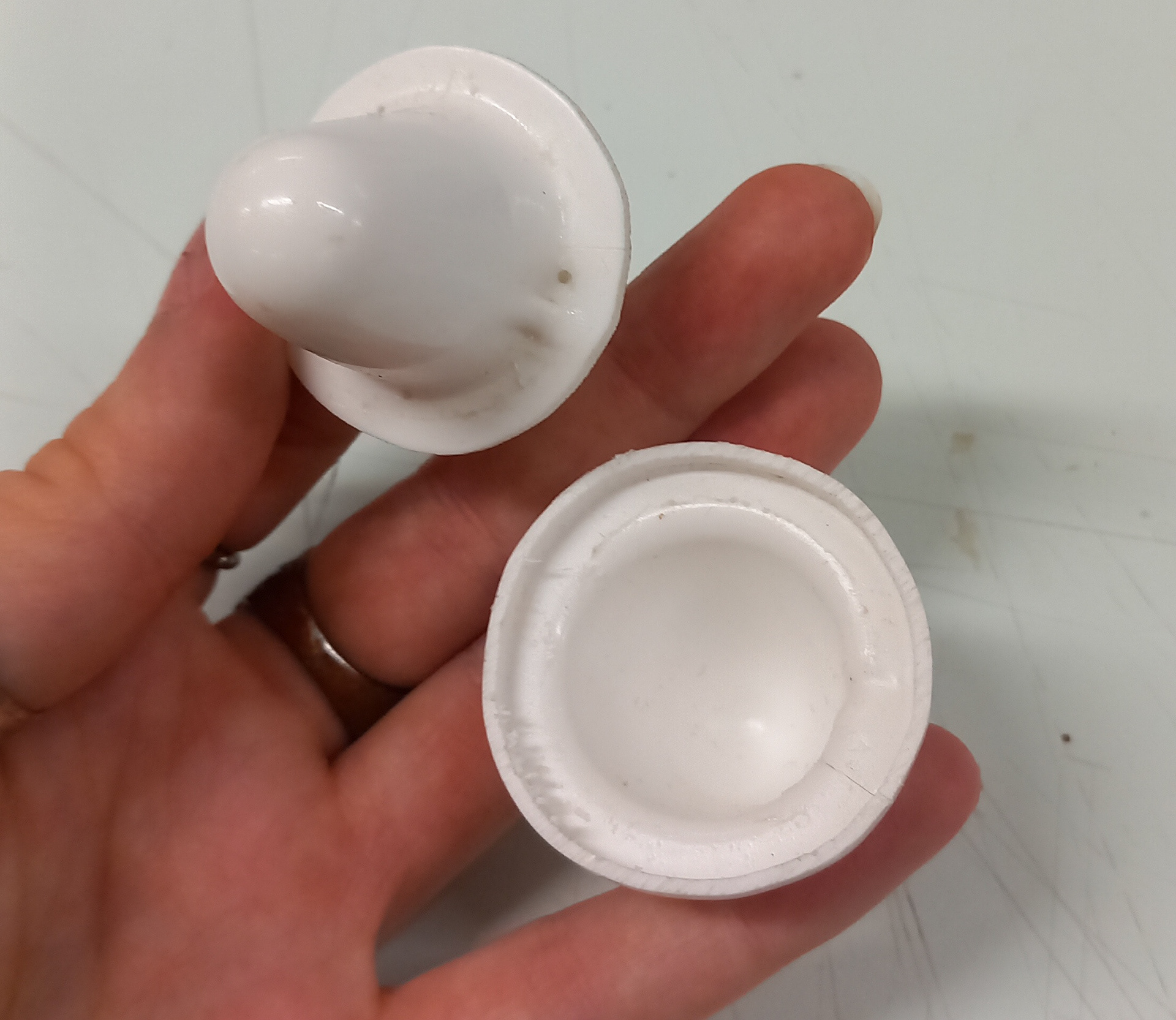
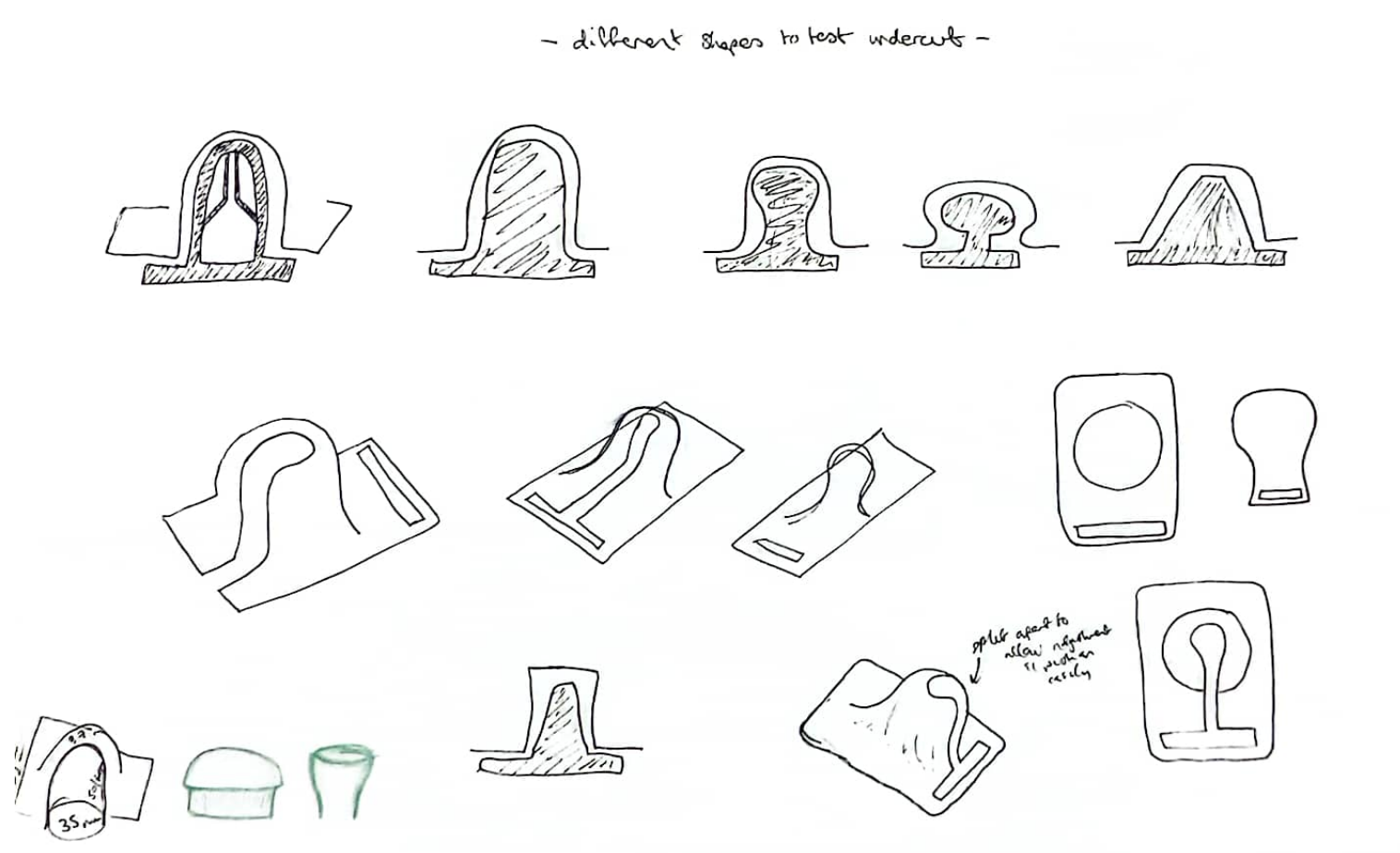
Sketches of shapes to test
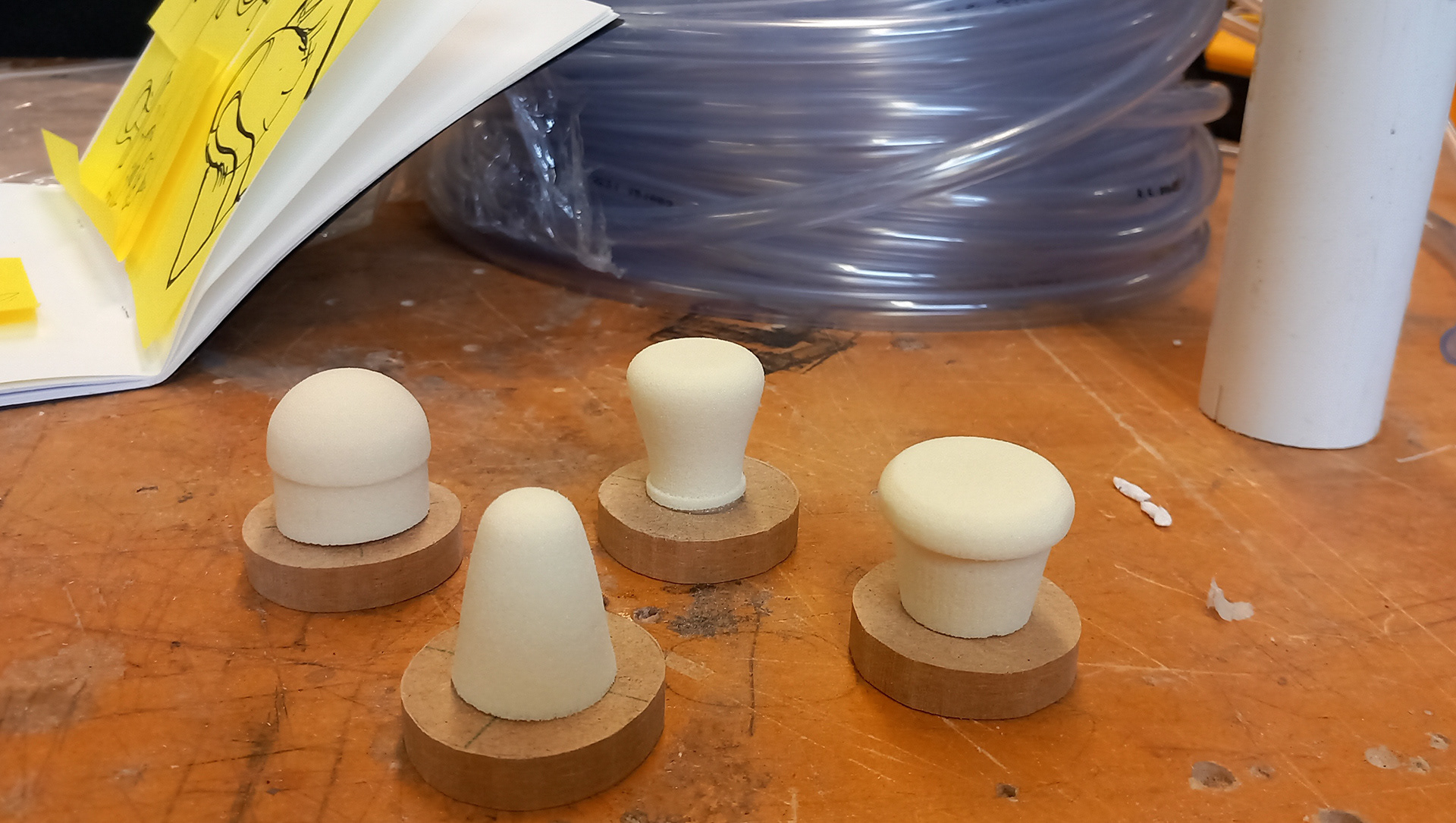
Componont one models (pre-vacform)
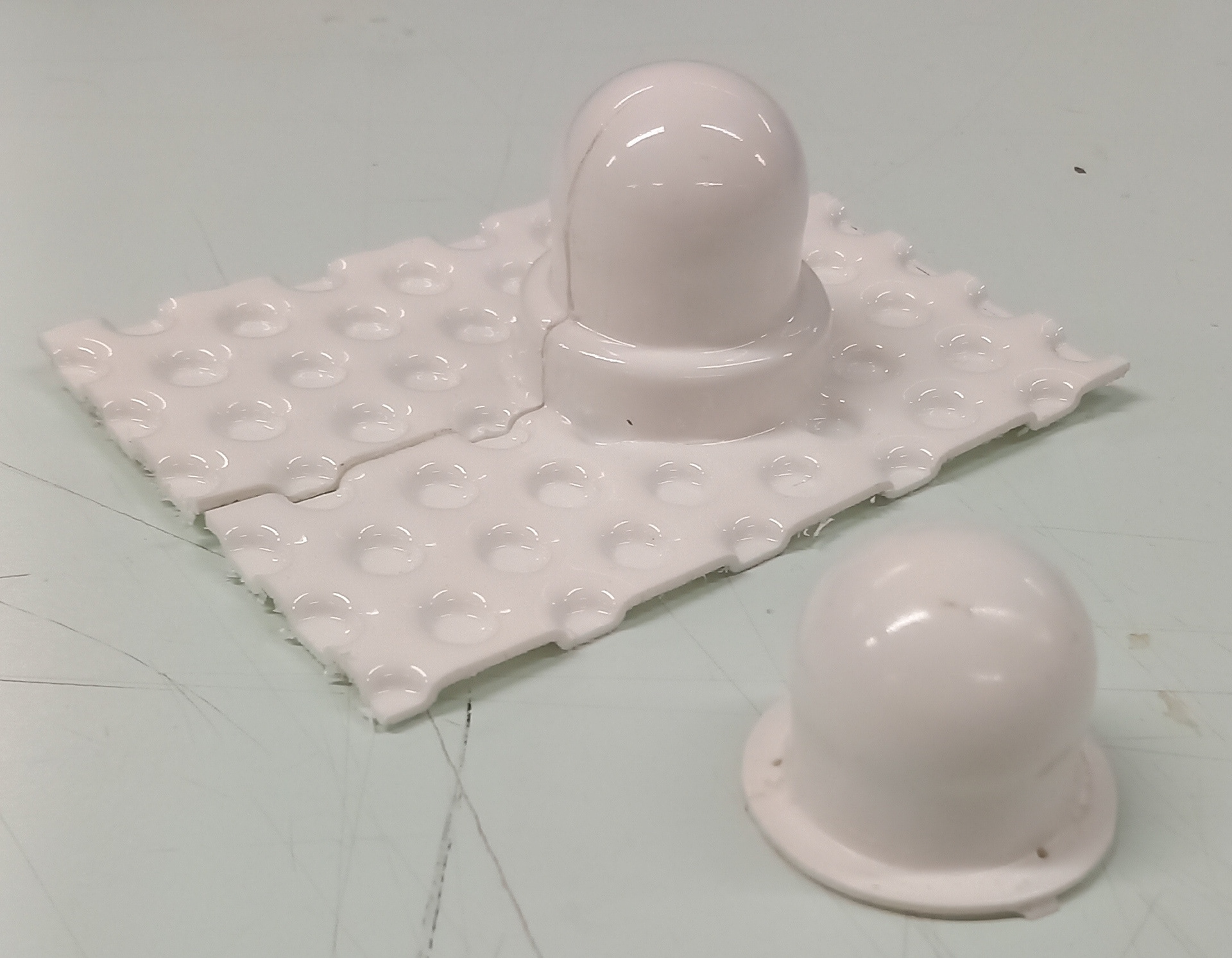
Test 1 - component 1 & 2 ( post-vacform)
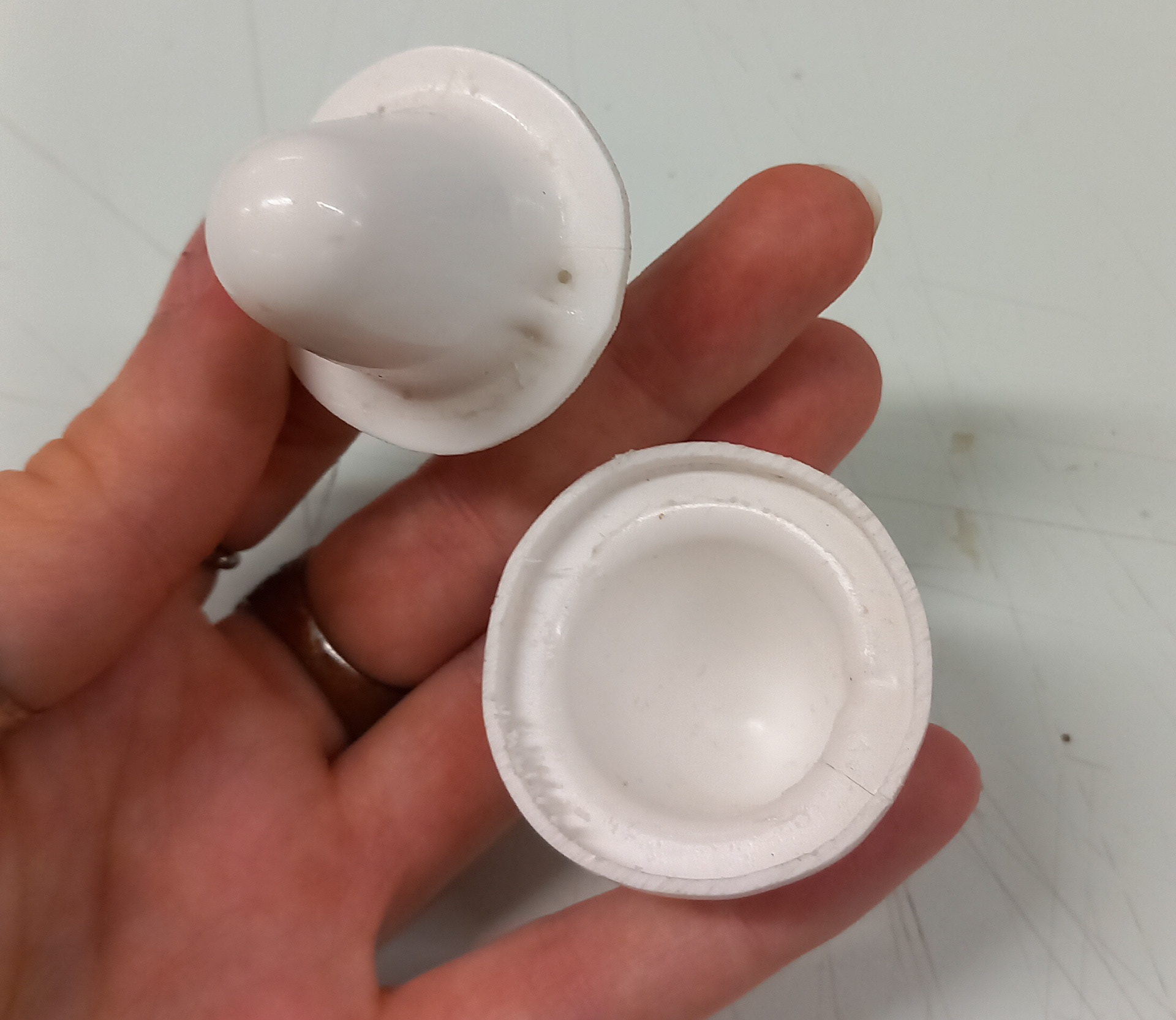
Test 2 - component 1 & 2 ( post-vacform)
Outcome
After continuous re-evaluation through sketching, prototyping, testing sketch models with actual guitars, digital sketching and modelling I finally made a CAD model using my limited and ever developing skills to translate my design into a model that could be sent to manufacturers to help receive a quote for moulding the components.
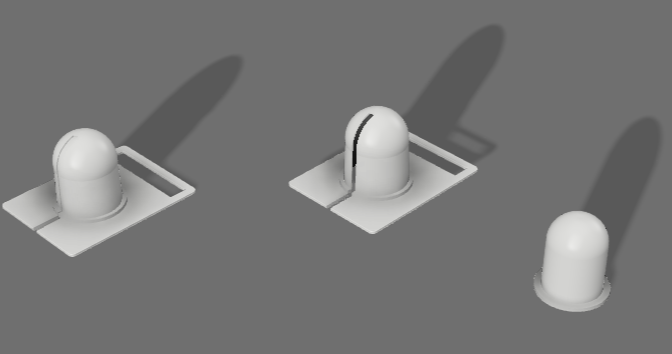
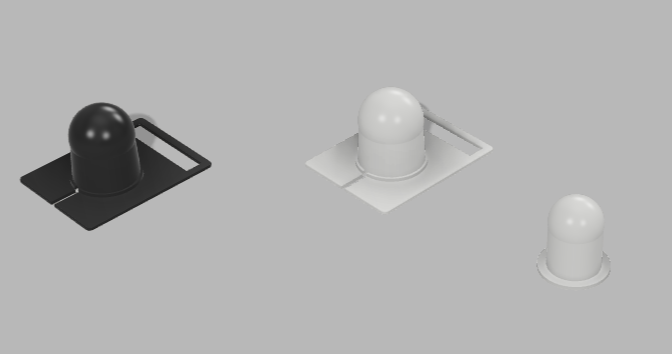
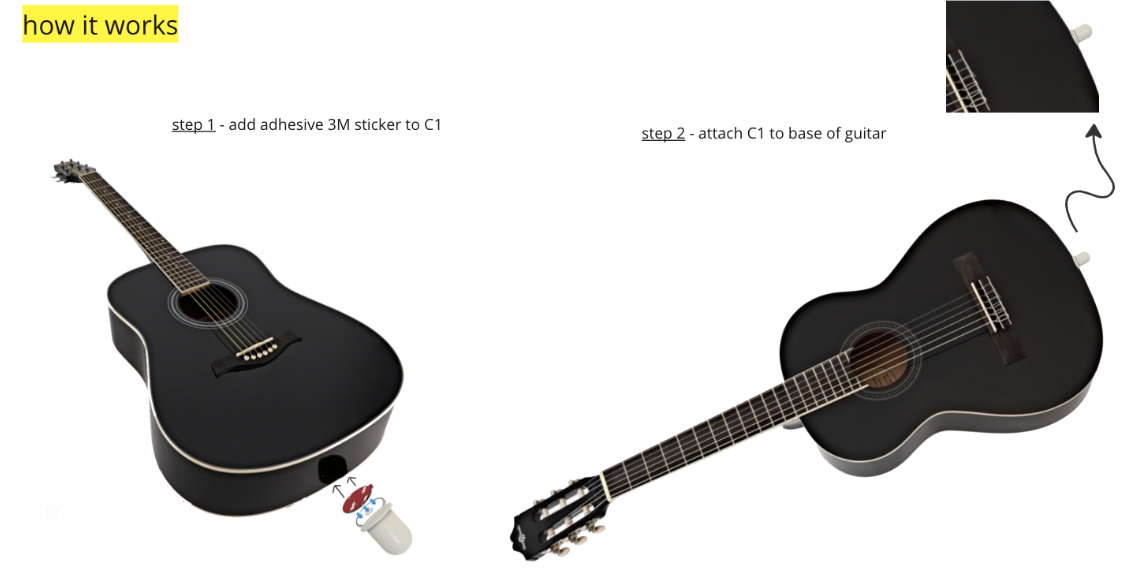
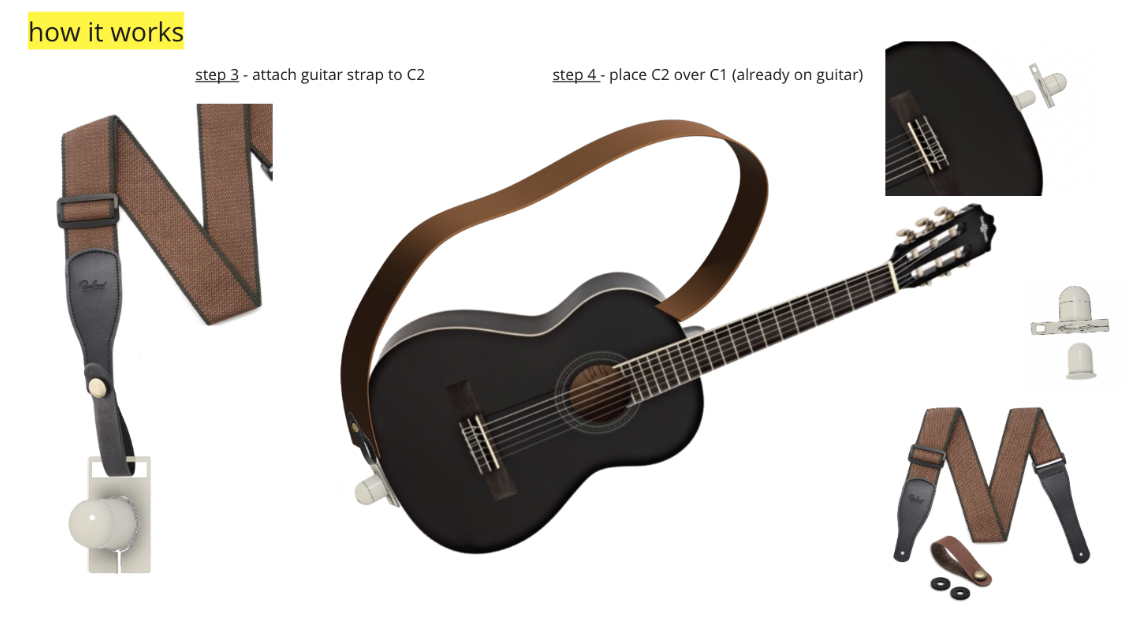
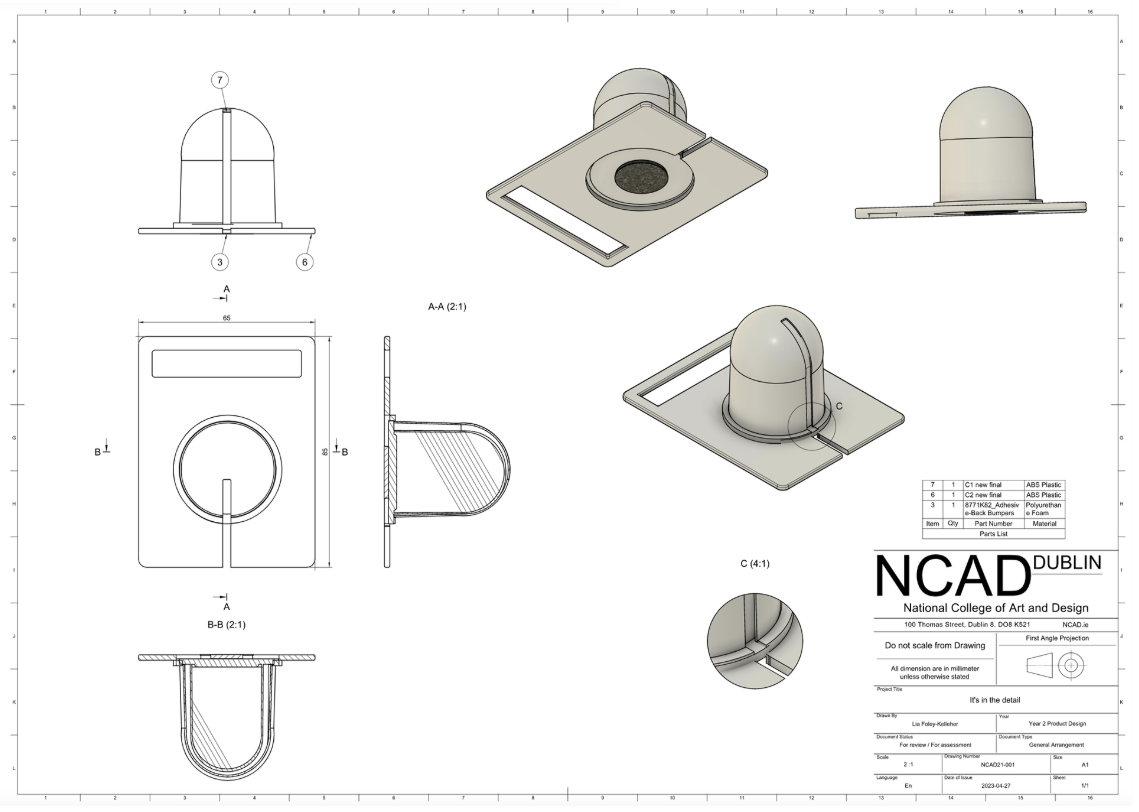
GA drawing
Details
I decided to use ABS to manufacture these components due to its durability while remaining relatively lightweight allowing this product to be used for a long time across various instruments. I chose a gloss white finish in order for this product to stand out in illustrations yet match any colour guitar. If I were to send this product to be manufactured I would choose gas assisted or electric injection moulding so many items could be made quickly and accurately therefore hopefully reducing cost compared to the quotes I received for 3D printing which would be more time consuming. My chosen off shelf component is a high strength transparent, gel reusable sticker allowing for easy de/attachment to the base of the guitar. Market price for the 'Snap' guitar strap attachment would be circa 30 euro (2 component pack).
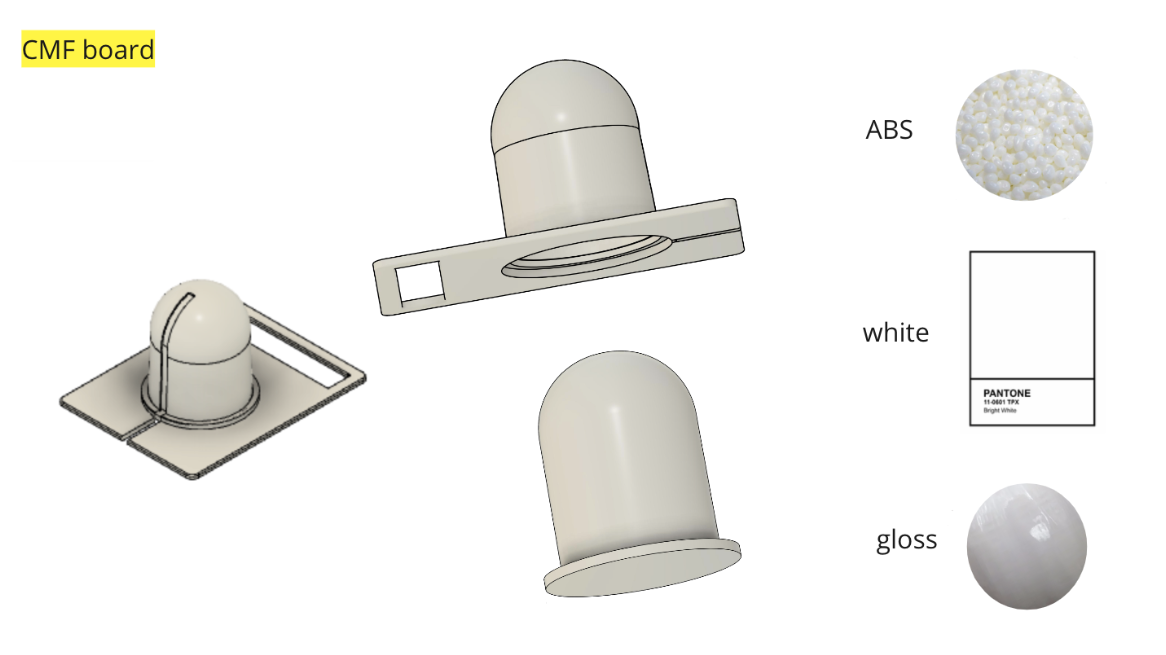
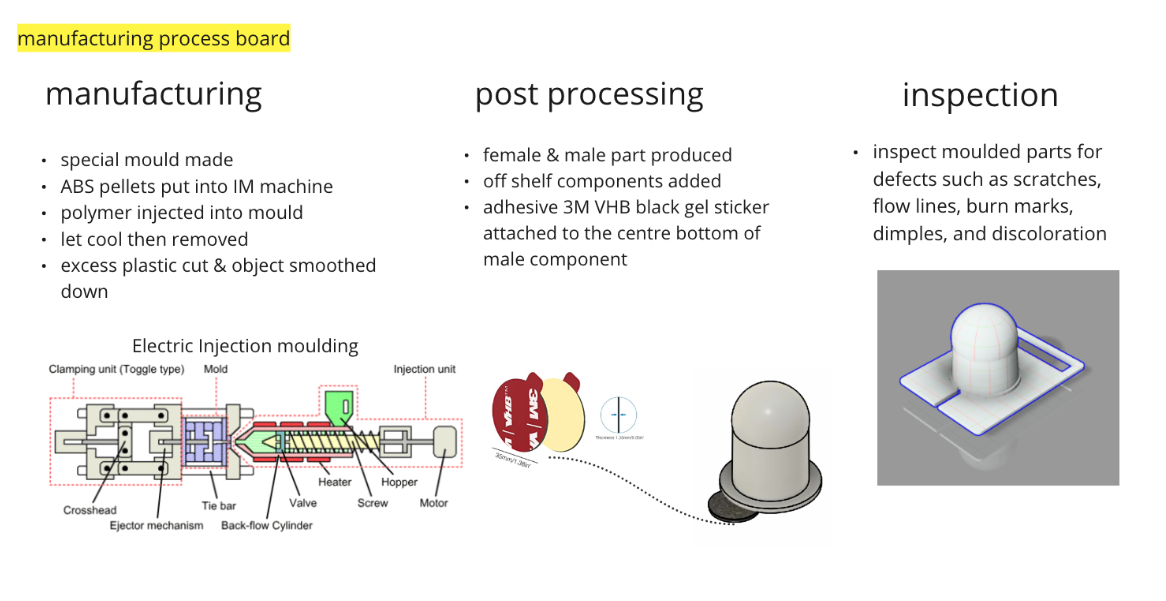
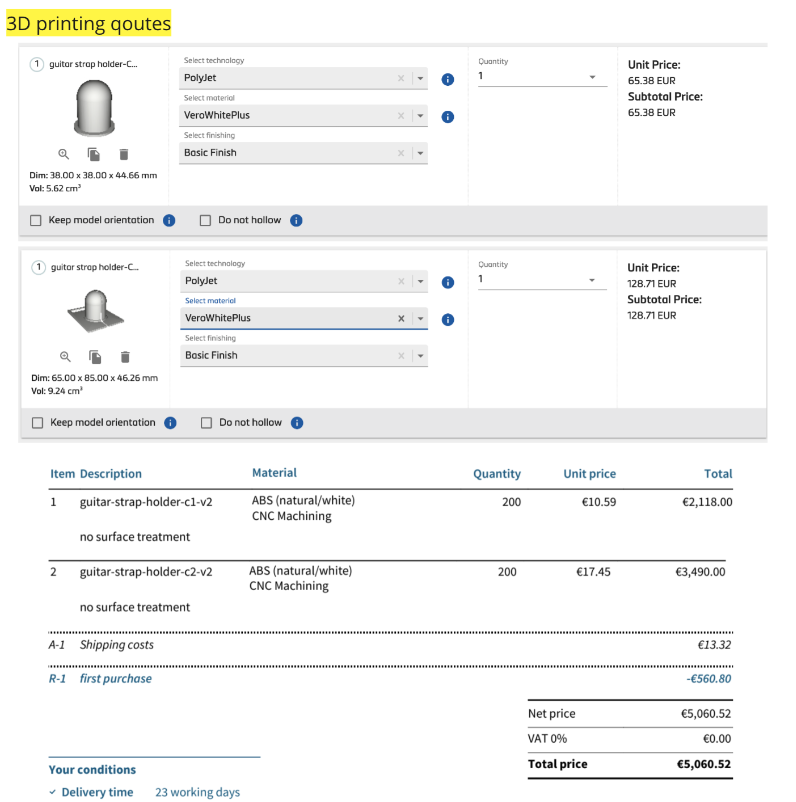
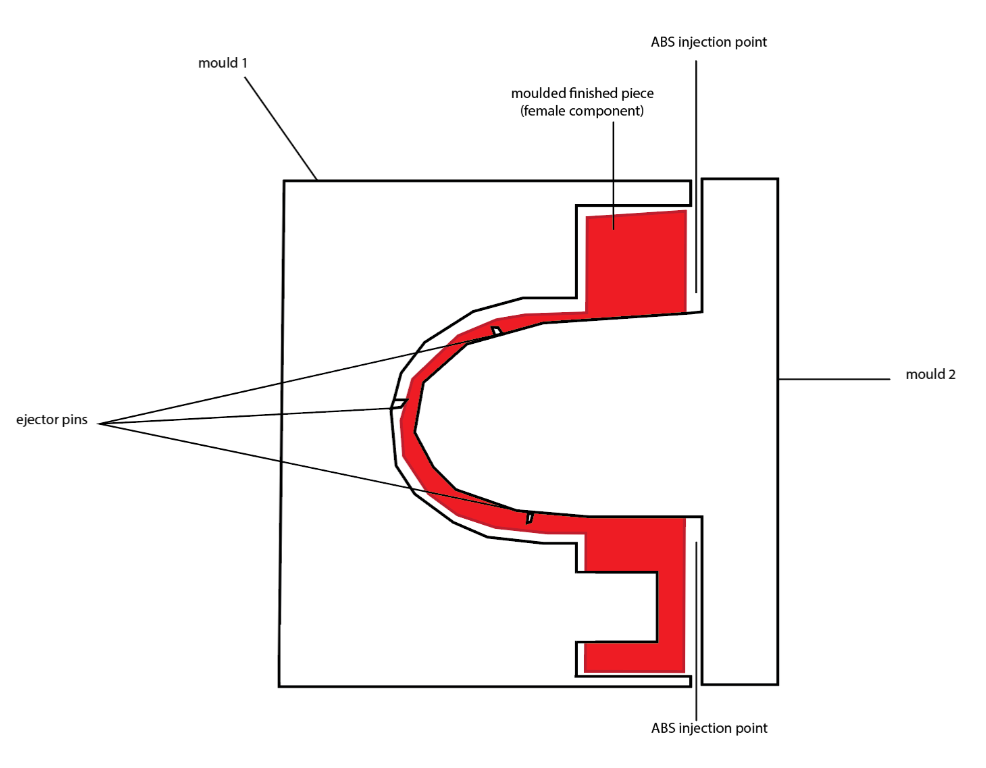
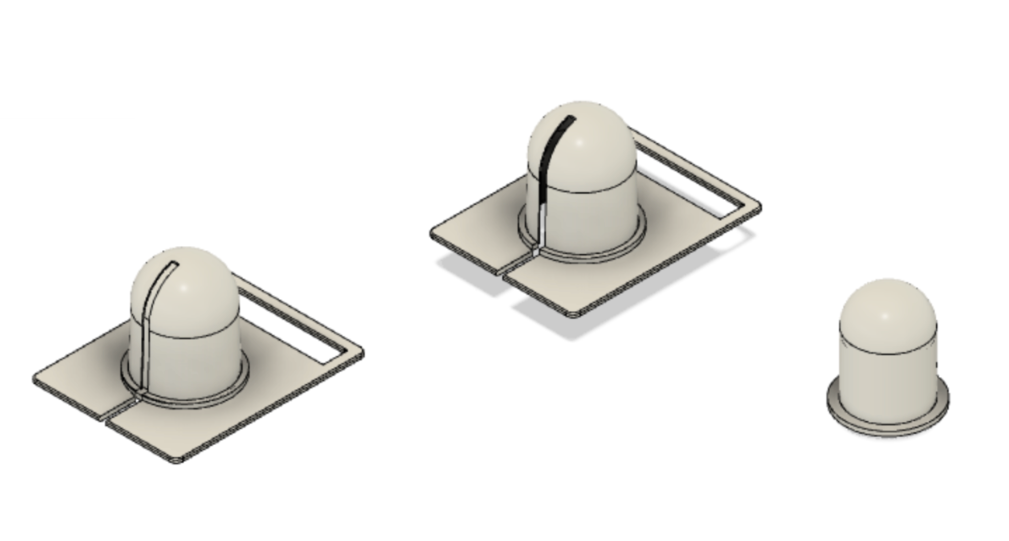
Reflections
Overall I was quite pleased with how I handled this project given the development in my ever developing CAD skills and learning more about various manufacturing processes and designing for manufacturing and how every line or minuscule design decision aspects all forms of production value and further I believe through the multiple sketch models I made I was able to back up my decision making and design reasoning as well as considering form and proportion in relation to the average guitar (which I was designing for) and ergonomic comforts.